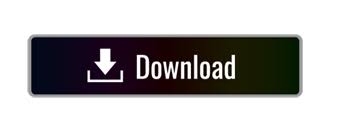
Non-motion control rated jaw couplings are great for this as the "spider" durometer can be tuned to dampen the load. Other applications care not about backlash or compliance, but require large misalignment tolerance or vibration damping characteristics. These tolerate very little misalignment (although any misalignment is intolerable because it can cause the universal joint surging of motion, even at small scales, which is usually undesirable). In precision applications, zero backlash and ultra low compliance are key which necessitates precision couplings. Different applications require very different couplings. Not to go off topic, but shaft couplers are a very interesting topic. Lol.) Also need to clean up the wiring and start planning a partial enclosure. ( I kind of wanted to have it like the 2 axis mill power setup I use at work and since I mainly have been running wire edm for the last 10 years. I struggle to get fusion360 to post toolpaths with zero Z moves. Short term changes are going to be upgrading to Mach4. And hopefully I can improve the backlash of the Y axis some. So since I tried to keep my hand wheels the table moves opposite as it normally would cranking it. Overall I’m pleased with the machine, the only complaint I have is the Y axis ballscrew is not left hand thread. as I’m typing, I realized I can swap the couplers to check there.Īlso, in Mach 3 is there a way to use my homing switch as a limit switch or do I need to have two limits and a home switch for my x and y. So my question is can I or should I try to shim in between the double ball nut? Is it possible to have that much play in the shaft coupler? What else can I do to improve this?. I tightened the lock nut till I had maybe.
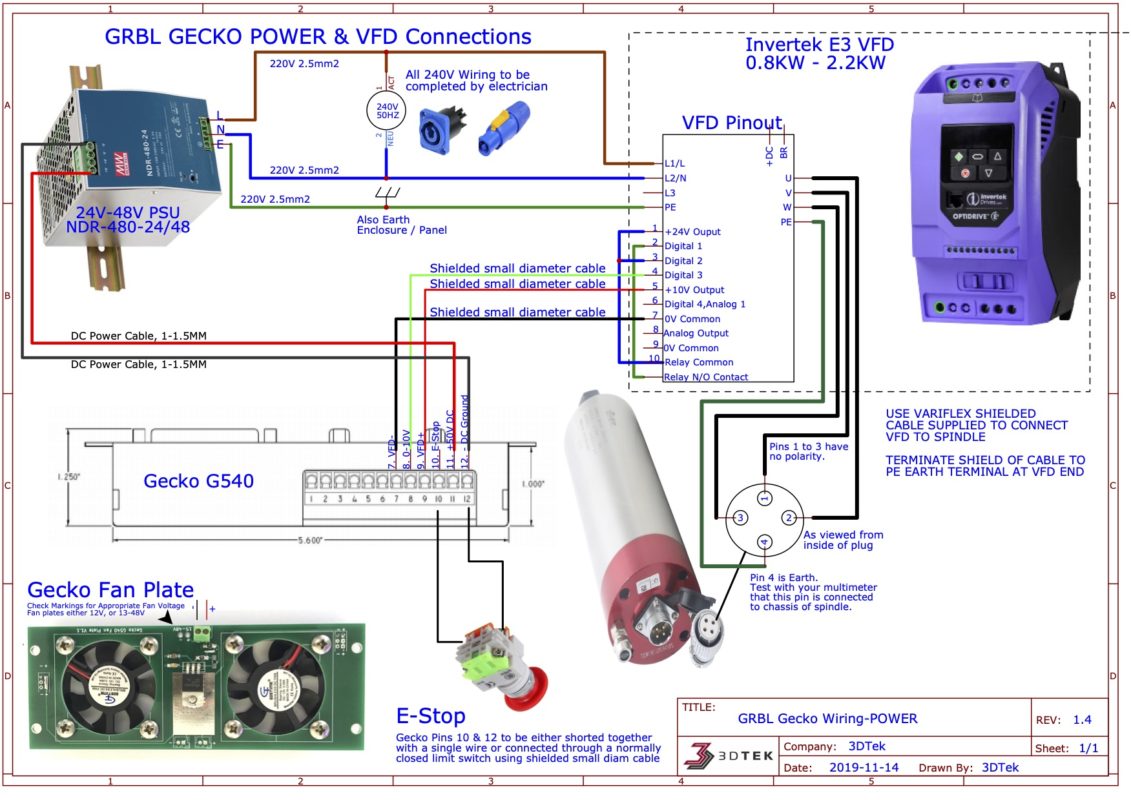
X is acceptable to me but Y seems like a lot. Everything bolted up as it should with no issues so far. I’m happy with the CNC kit and can say the cast iron mounts were worth the 8 month wait.

Right now it’s only 2axis with 570oz dual shaft steppers with a sepraty DRO. G540 running Mach3 on an old desktop using the parallel port. I had a couple questions in another thread, but didn’t receive any feedback so I started a new thread to hopefully get a few answers and some feedback.įirst, a little bit about my setup.
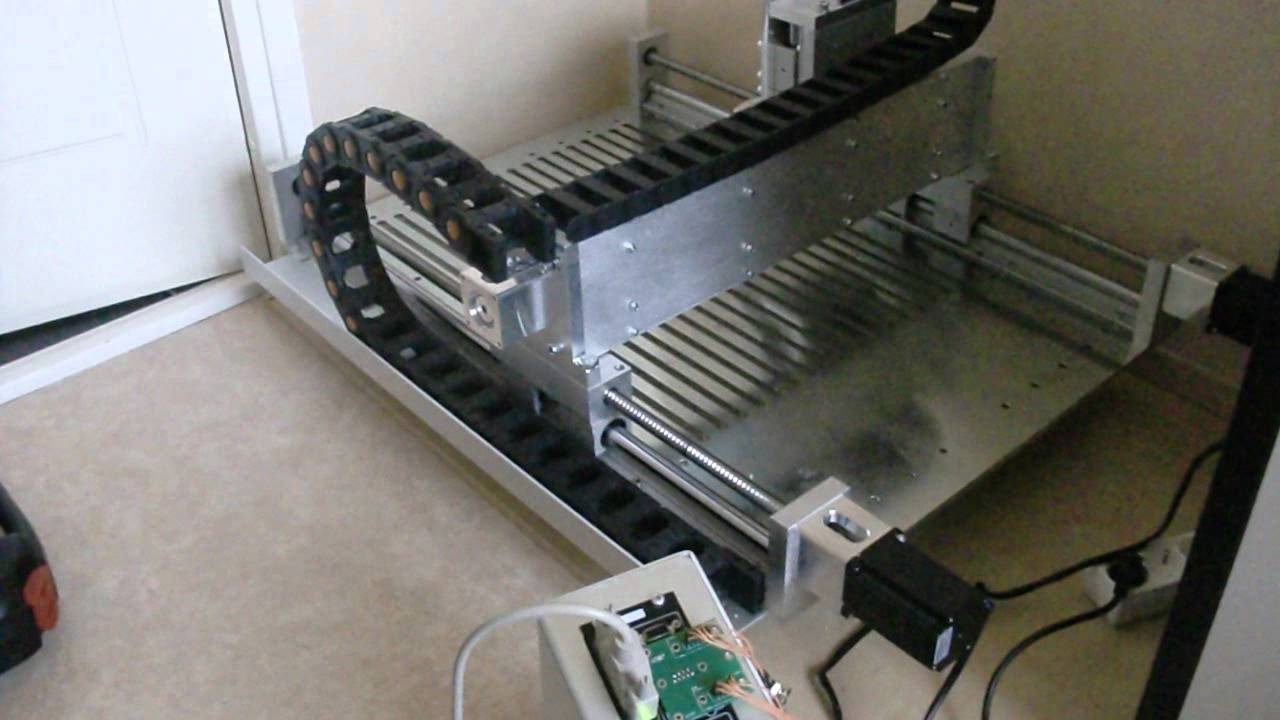
#DUAL X AXIS WITH GECKO G540 DRIVER#
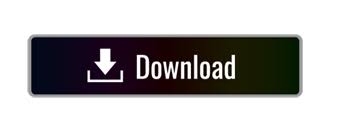